It would be a major surprise if the 2016 McLaren-Honda was not a huge competitive step forward from its woeful forebear. Honda has understood the limitation in the energy recovery rate of last year’s power unit, knows the source of the problem and will undoubtedly make major gains at its second attempt. The company’s motor sport boss Yasuhisa Arai has confirmed it will be retaining the ‘size zero’ concept whereby, uniquely, the turbine and compressor are small enough to be located within the vee of the engine. Given how quickly energy transfer efficiencies are improving in the F1 hybrid era, however, it could be that the size zero concept is already forming a long-term limitation to Honda’s power unit. The concept might already be obsolete – and becoming more so all the time as those efficiencies improve further!

To purchase the lead image click here.
Why size zero might be obsolete
Mercedes engine boss Andy Cowell outlined how Mercedes decided upon the sizing of its turbine and compressor: “It’s down to the level of efficiency you’re going to achieve from all the bits in the turbo compound loop. If you think that the electric machine – the power electronics and the MGU-k – can’t be that efficient, then there’s no point having a big turbine. Because the lap time simulation is based on what the ‘k’ adds to the crank. If you think you can get 100kW from the turbine into the MGU-h, but you’re only going to have 50 by the time you get to the crank and you look at the weight and volume of all the cooling systems to deal with that wasted 50, that’s going to start outweighing the advantage of a bigger turbine.”
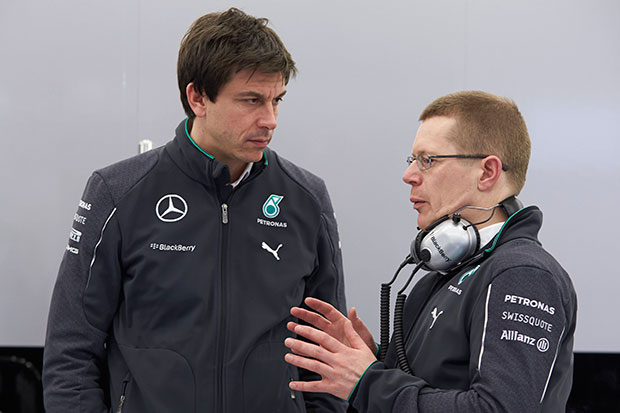

On the Mercedes the compressor sits outside the vee. The turbine and compressor have been made bigger each year to take full advantage of the increase in energy transfer efficiencies in that turbo compound loop. Reflecting the newness of the technology, those efficiencies are increasing at an incredible rate. When KERS was introduced in the V8 era, about 39 per cent of the recovered energy made it as far as the crank. In 2014, the first year of the current formula, that had risen to 85 per cent. It is now at 95 per cent – for Mercedes, at any rate. The thermal efficiency – how much of the fuel’s energy content is delivered to the end of the crankshaft – of the standard-setting Merc is already at 47 per cent, compared with 40 per cent for the 2014 unit (it was about 29 per cent in the V8s).
At the levels of power the Mercedes is now recovering and converting, the compressor would be too big to fit inside the vee. The advantage of limiting the size of the turbo so as to place it between the banks of the engine’s vee are that it makes the whole unit significantly shorter – and a look at the McLaren in plan view shows that it had by far the most tightly packaged rear end of all the 2015 F1 cars, giving the biggest potential for aerodynamic exploitation. The more tightly waisted the ‘coke bottle’ section of the bodywork can be, the faster the air can be made to flow – as the pressure change induced by that waisted profile accelerates the air. The faster the air flows over the downforce-producing surfaces – rear brake ducts, diffuser top and the accelerating effect on the wake behind the rear wing – the more downforce will be produced. There can also be an aerodynamic benefit from having the rear wing further away from the blocking effect of the engine cover.
So the trade-off becomes how much lap time can be derived from the aerodynamic benefits of ‘size zero’ versus the lap time benefits from the greater energy efficiency (typically utilised as ‘more grunt’) possible from having the bigger compressor sitting outside the vee.
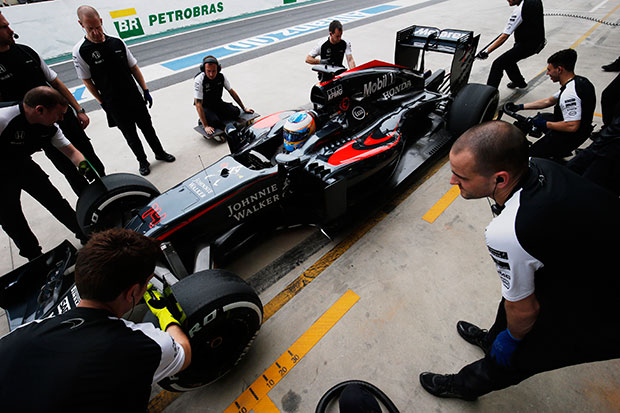

The crucial question for McLaren and Honda is how well its combination of power and aero correlates with state of the art and whether Honda has accurately anticipated the efficiency and power gains as technology is advancing. Has the technology of the Honda’s compound loop advanced so that it, like the Merc, can convert as much as 95 per cent of its recovered energy to the crank? If not – and the peak efficiency size for its compressor still allows it inside the vee – can it get close enough that the power shortfall is at least equal to the aerodynamic gain?
Last year Arai-san allowed that the 2016 power unit would feature a bigger turbo, but that it would still be situated inside the vee. He estimated that it would be ‘around the same size’ as the 2015 Mercedes turbo, “Though without knowing what development Mercedes will make, of course.” Well, now we do know that Mercedes has indeed developed further and increased the turbo’s sizing – as Cowell confirmed last week in a press briefing at the Brixworth Mercedes HPP factory.
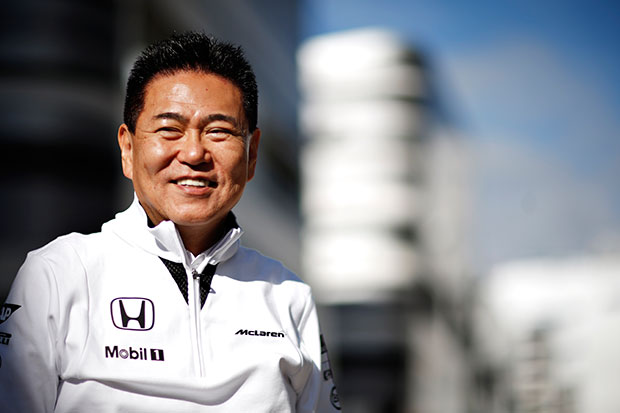

Which poses an obvious question. If, from the perspective of power unit performance, the optimum sizing of turbo is now beyond that which will fit inside the vee (as seems to be the case), is it still possible to overcome the lap time cost of that through the aerodynamic benefit the Honda layout allows? And even if the trade-off is currently closely balanced (which it might not be – it may already be heavily biased in favour of the Mercedes layout), then isn’t it going to develop further away from ‘size zero’ as efficiency gains continue and allow yet-bigger compressors?
Why the 2016 size zero should be vastly improved
The sizing of the turbo is crucial to the whole power unit’s efficiency, and was at the root of the Honda’s shortfall last year. A smaller turbo (turbine plus compressor) has to run faster than a bigger one for the equivalent benefit. But even though the Honda turbo was capable of running beyond the 95-100,000rpm typical of those on the Mercedes, Ferrari and Renault (there is a regulation limit of 125,000rpm for the ERS-h that’s typically situated on the shaft joining the turbine and compressor), it reached an efficiency ceiling at a speed lower than that. “The problem was the efficiency of both the turbine and the compressor,” conceded Arai. “At the speed it needed to run, it was inefficient.”
Honda is working against a limitation relating to the exhaust gas pressure created by the turbine. Back pressure steals power from the internal combustion engine. Obviously, the turbo creates more power than its back pressure costs, but there is an optimum efficiency point at which the greater back pressure created by greater boost is not worth it – particularly in a formula where there is a regulation limit on maximum fuel flow and the total amount of fuel used during a race. A slower-running, bigger turbo allows that optimum point to be potentially higher.
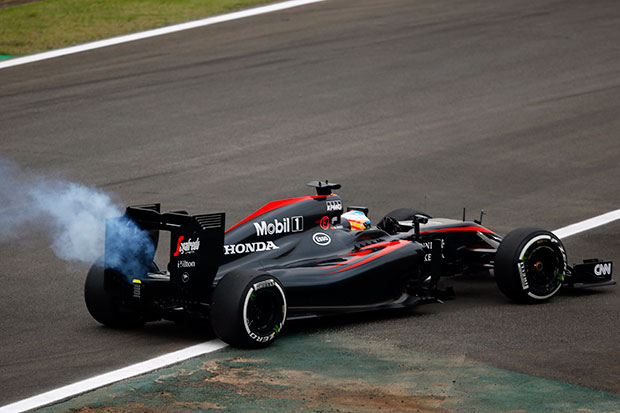

The turbo of the 2015 Honda could not be run fast enough to overcome its smaller dimensions. The limitation imposed by the fuel-flow regulation could not be reached before the Honda hit upon the cliff face loss of efficiency imposed by the mechanical loop of the turbine/compressor/engine. It had arrived at the point where running it faster delivered less than it cost. The point defined by that lack of efficiency was at a place where the Honda ERS could not adequately harvest and deploy.
At the speed at which it was limited by its inefficiency, the small Honda turbine didn’t allow the ERS-h to harvest much more than 40bhp-worth of the 160bhp permitted. Any track with full-throttle running of more than 33sec would potentially use up all of the battery’s stored power within that lap. On tracks with more than 33sec flat-out running, the ERS-h would be set so that what power it could contribute was available throughout the lap, in which case it would be contributing less than 40bhp under deployment.
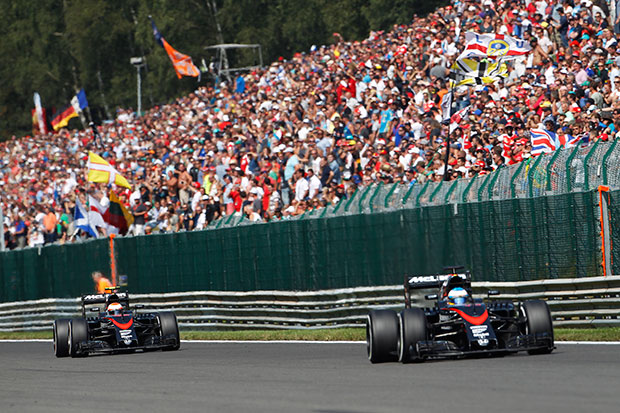

At its efficiency-limited turbine speed the small 2015 compressor could not adequately compress the intake charge. Nor was the small turbine efficient enough adequately to harness all the exhaust heat. Poor turbine performance = poor compressor performance = less explosive combustion = less exhaust heat being created = less heat for the turbine to work with. The inefficient turbine meant it was not even making the most of the relatively little heat it received. That whole mechanical loop could not then capture and supply enough energy to feed the battery – so reducing the effectiveness of that loop.
The key to it all is generating more oomph from the turbine and compressor, as the electrical recovery is largely (though not solely) a function of that. From GPS analysis it would appear the internal combustion part of the power unit’s performance was only about 40bhp down on that of Mercedes – and actually slightly ahead of Renault.
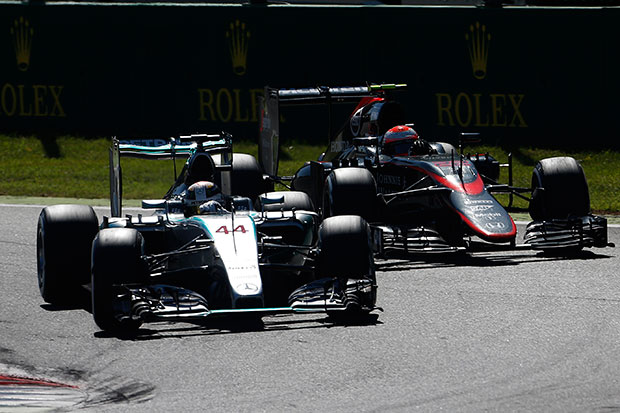

Part of that increase in potency will come from an increase in size of turbo (turbine and compressor) – up to “about the size of” the 2014 Merc unit, as Arai has it. But beyond that, the efficiency of those spinning units is being intensely studied. “We are looking at many different turbo designs,” Arai said towards the end of last season.
From the archive September 2015. Mark Hughes explores F1 engine woes: The power struggle.
The blade designs inside the turbine and compressor are hugely complex works of art, with variable radii and double entry volutes (the section that receives the gas or fluid before it’s pumped by the impeller) for compact packaging and optimal gas dynamics. Optimising these will be crucial, but having the energy conversion efficiency to justify the biggest turbo it’s possible to install within that vee should be the key that will transform Honda’s competitiveness in 2016.
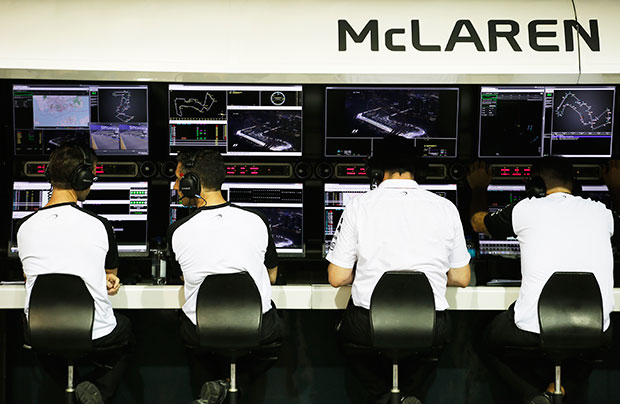

But in the task of taking on and beating Mercedes in the longer term, is Honda going to have to rethink the basic zero size premise of its power unit? Now that the engine development token system is set to be abolished from 2017, perhaps that’s what the R&D guys in Japan are already working on…