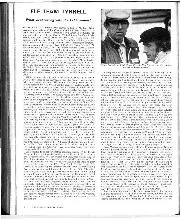
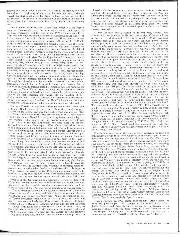
ELF Team Tyrrell
What went wrong with the 1972 Season ? With the 1972 Grand Prix season ending at Watkins Glen everyone was praising Colin Chapman and his John Player Lotus team, with…
The first thing you see upon entering the offices of PhysicsX is an 800cc two stroke motorbike powered by a snowmobile engine. Next there is the Kellison EXP001, the Batmobile-style racer that sprang from the mind of Jim Kellison in 1957 and which has recently been restored. Further inside the offices the walls are crammed with textbooks and patent plaques.
“This is about heart,” Robin Tuluie says about the Kellison before gesturing to the book-lined office. “In there it is cerebral.”
Tuluie is one of the great maverick engineers – some would say visionaries – of his time. He started out as an astrophysicist, before swapping planets for pitlanes and taking a variety of jobs spearheading new innovations with F1 teams and helping secure a world championship for Renault in 2005. He has also been applying his scientific mind to MotoGP. Along the way he has raced his own bikes to US national championship wins and created the one-off snowmobile-engined Tularis 800 that takes pride of place at his new offices in Bicester Heritage, Oxfordshire.
In 2005, Fernando Alonso won his first F1 world title – partly due to the Renault R25’s tech
Today PhysicsX has broadened its areas of research to encompass aerospace, medical devices, electric vehicles, renewable energies and motor sport. It describes itself, a little mind-bendingly, as “a deep-tech company of scientists and engineers, developing machine learning applications to massively accelerate physics simulations and enable a new frontier of optimisation opportunities in physical design and engineering.”
To give an idea of the breadth of its work, current projects include the invention of a scalable mechanical heart and optimising a large hydro-turbine. Breaking new ground is Tuluie’s speciality and he has Formula 1 world championships to prove it. He has the banned components, too, like all the best racing engineers, and he wears them like badges of honour. Both the tuned mass damper which Renault used so effectively in the mid 2000s and Mercedes’ FRIC suspension system of 2013-14 were banned more for their unfair advantage rather than for being outright illegal.
As well as tackling engineering conundrums off track, Robin Tuluie can often be seen on track – here at Silverstone in 2021
At Renault, what was initially a problem became a championship-winning gain almost by chance. “Dino Toso, our head of aerodynamics, called me about a wind-tunnel instability,” Tuluie recalls. “The car bounced laterally and yawed a bit as it was getting up to speed. I looked at this and said, ‘Oh, it’s just like a building in the wind. We just need a tuned mass damper.’ I knew that because of Neil Peterson, a really phenomenal engineer at [American research corporation] MTS. When you walked into his office there was this model of a building with a tuned mass damper: Neil and his team had invented it for the John Hancock Tower in Boston.
“We created a little simulation model, utterly basic, just to reproduce it, and optimised the positioning. A few teams from R&D were involved, Frantz Jourda was a model analysis expert we brought over from the mothership at Renault, plus Phil Charles and Dave Hamer who ran the seven-post rig. It made its way into the wind-tunnel car and was just fantastic. It solved the problem. Bob Bell then walks into my office, sits down and says, ‘Do you think you can make it work in the car?’ It was a question not of legality, but would it work in the car and will it help? So we turned it sideways, so not for yaw but pitch, put it in the nose on the seven-poster car. It was three-tenths of a second quicker.”
One glance at the walls of PhysicsX will tell you what happened next: Fernando Alonso cruised to the 2005 world championship and was well on the way to another when the system was outlawed.
Tuluie’s problem-solving was able to turn around the fortunes of Renault
“It was declared to the FIA because it was in the crash structure,” says Tuluie, his animation increasing. “Then in the middle of 2006 it was a big problem. By a process only known to the FIA it was declared illegal because it moved and had an effect on steadying the car. There was some technical back and forth, but perhaps the most compelling thing is that when you go over a kerb and the wheel goes up in the air, the tuned mass damper moves – but without input from the road. The rule is suspension must respond to the forces at the contact patch, so they ruled it illegal. To which I replied, when the car is up in the air the wheel and tyre are a mass suspended from the chassis by a spring and resonate without applied force. In any scenario you can dream up that it was illegal, you have a very equivalent symmetrical argument why it was legal. There were no technical grounds, none whatsoever, that it should have been made illegal.
“The thing is, we were quick. We were competing against the big established teams. We had great drivers and great people; everybody pushed in the same direction. We were doing cutting-edge stuff: the Renault engine was phenomenal, we were doing super work on the chassis side. Put all that together and you don’t have a weak link in the chain. You win the world championship.”
The key to Renault’s success was its mastery of simulation. And this is the area that Tuluie was expert in. He had mastered the art while working on the Tularis motorbike during the late 1990s. To build the race-winning screamer, with its carbon fibre gearbox casing, clever suspension and ultra-light weight, he says he fundamentally changed the engineering process. “I had no experience, but I knew something about physics and I knew something about simulation. It might have been the first time the fundamentals of a motorcycle were determined by simulation only – I presented it as such at an international SAE conference. I learned early on that if you do the simulation right and implement the laws of physics into code correctly that you can predict behaviour. The moment you can predict correctly, nine-tenths of the battle is won.”
Simulation techniques used on Tuluie’s Tularis motorcycle in the late 1990s transferred to F1
He applied these lessons to Renault a few years later and to the corner of Enstone that housed Tuluie and his self-described skunkworks. A ‘hydro-pneumatic midfront’ appeared to be the solution. “It was a tiny computer, purely hydraulic, pneumatic and mechanical,” continues Tuluie. “Just a central hydraulic spring between the two elements, no sensors, but it could tell the difference between a straight or a corner from the history of displacements and forces that occurred. But it had 10 or 12 different adjustable features, so we needed to simulate it. We chose Modelica. Jonathan Allen in R&D wrote the model and it was fantastic, then we used an optimiser and cranked through hundreds and thousands of set-up optimisations. Even on a seven-poster you can’t do that.”
After a few races it was dropped because of instability under braking and so came a pitch-couple system. “Dave Hamer had the idea of connecting the car from front to rear and across so we could make the car soft in pitch but stiff in heave. We ran it on the seven-poster for the first time and it was a disaster. Then we realised the lines had been connected the wrong way round. It was stiff in pitch and soft in heave, so it was crap in grip and crap aerodynamically.”
As it began bearing fruit, Tuluie left for Mercedes, where a separate system was in development. “We just accelerated very quickly from that into FRIC, which was again a pitch-coupled system with the front and the rear interconnected. This small hydraulic computer had become a lot more complicated – it looked like a little nuclear bomb, or what they look like in a movie. We could keep the front ride-height of that car exactly where we wanted, around the whole track, within a millimetre. Anywhere. It was really awesome.”
After his time with Renault, Tuluie returned to his previous field – motorcycle racing, with Ducati in MotoGP
“The only thing in common was the starting principle of having a front cylinder and rear cylinder connected,” he reiterates. And that it would eventually be outlawed. Then there was Bell and Tuluie. They had met when the latter worked for MTS in America, his adopted home after moving from Germany in the 1980s. Once again, the link was the Tularis: “I gave Bob a lift back to the airport in my old van and he said: ‘Have you ever thought about living in England?’ I thought: ‘I know what he’s asking.’ I said, ‘Well, I haven’t and I’d love to but right now I need to race my motorcycle.’” The bike was in the van, taken specifically to show Bell, and the decision to stay yielded race wins in the competitive national series. “I ended up doing some consulting work and we had a chat in his office,” continues Tuluie. “He asked me how I was doing and I told him that I was getting a bit bored.”
Years later, at Mercedes, it would be Ross Brawn tasked with reuniting Tuluie with Bell. “Ross said to me: ‘We know how to make the car lighter, incrementally faster, all that. We don’t really have someone looking after our innovation projects – our non-sausage machine projects. We have a good sausage machine. We need someone to look after the non-sausage machine.’ We had to think of a title so John Owen, our chief designer, and I decided chief scientist would be good. Nobody really knows what that is and it doesn’t look too hierarchical. It gave me free rein to go and talk to anybody and get involved with anything I wanted to. It was non-threatening and I had a lot of fun and impact.
“At Renault we would develop things in R&D, then bring them into the design office who might or might not find them appealing. At Mercedes we were much more integrated, designing and simulating all of the things as a team. Organisations evolve. What we had at Renault was phenomenal, but as a Formula 1 team migrates from a race team to a technology corporation, the structure also has to migrate and change. That was clearly recognised at Mercedes. With leadership like Ross and Bob success was inevitable.”
Tuluie gave the Goodwood crowd a taste of the 800cc Tularis at 2005’s Festival of Speed
The motorcycle itch remained unscratched, though, having turned down Yamaha for Mercedes when he left Renault. An opportunity arose to work with Ducati via Bentley, under the umbrella of the VW Group. “As director of vehicle technology I was tasked with transforming Bentley from traditional engineering to simulation-led engineering. It was a great opportunity and a necessary experience for what we do now, to understand how an OEM’s engineering process works and how to improve it. Totally different to F1, but much more akin to other advanced industries. At the same time, I worked with Ducati as a senior adviser working on simulation and innovation. The old love came back.”
The Italian team being at the forefront of the category’s technology meant it was the perfect fit for Tuluie and offered him the chance to properly challenge himself.
“I had been in F1 for long enough,” he says. “A modern MotoGP bike has evolved so much more than specification on paper – it is very much about drivability, entry feel, the way the bike turns, the balance. It’s more difficult than F1. You have to understand the vehicle dynamics and tyre, which changes its characteristics with lean angle – but you can still simulate this. Riders position themselves differently, too: the aerodynamics between a driver and a car is minimal; between a rider and bike it’s huge. You have to infer everything, and so much of the performance is related to the feel and confidence of the rider to explore the limits.”
FRIC – Front and Rear Inter-Connected suspension – was used by Mercedes but was outlawed in 2014
As a consultant, it created a ready-made path to start his own company and in many ways decide his team’s own limits. “We get to decide what we work on – we don’t work on weapons or oil and gas,” Tuluie says. “We work on renewables, on weight reduction, medical, aerospace, space and generally making the world a better place.
“We are into our third year, we are growing like mad and are about to open our second office in London after having moved to a larger one here at Bicester Heritage in October last year. I think the whole team has this fire, is so deeply passionate about our work. It’s more impactful, more important and much broader than anything we did in F1, which is rather narrowly focused. And we hire the smartest and best people there are, mostly from disciplines well outside F1.
“Tom, one of our ex-Formula 1 engineers, described it as moving from a narrow spot lamp on your desk to flinging the doors wide open to let the sun in! But the passion that motor sport ignites for engineering and the speed of development that it demands brings a way of working that is quite challenging but also extremely satisfying. We wouldn’t be here without it.”
Battle-hardened by F1, PhysicsX is still involved with motor sport