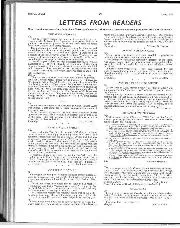
VW won the Safari!
Sir, Once again the daily press contains the usual grossly misleading large advertisements put out by the Ford Motor Company in connection with their efforts in the recent East African…
ALUMINIUM WHEELS FOR AUSTINS
After what seemed a period of neglect, the .blown Austin Seven has started to re-appear in races all over the country, particularly at Southport, where the suspension has proved particularly suited to sand racing, and at Donington, where Turner has made some meteoric circuits. An interesting newcomer on the Derby circuit last year was the tiny single
seater built by the Almack Engineering Services of Hampstead and driven by G. Abecassis. Continued research on this little car has shown it as capable of close on 110 m.p.h. The brakes haNie been modified to cope with these speeds, but Mr. Almack found that after two or three laps of the Brooklands mountain circuit, the brake drums became red-hot, so he determined to produce an aluminium alloy
wheel which would dissipate the heat and retain the brakes at their original efficiency.
Accordingly, in conjunction with a famous tyre manufacturer, an aircraft firm, and the famous Bramber wheel works, it has been possible to design a wheel, fully patented, which is a great advance over any previous design in alloy. The accompanying illustrations give some idea of the finished appearance, -which is very pleasing to the eye.
The wheel consists of three parts, each of different material. The brake drum is of steel chromium, which has been found to give the greatest frictional coefficient. This drum is machined inside and out, the outside machining forming a taper. This, in turn, forms a hub around which is shrunk an Aerolite buttressed casting of special alloy on the outer circumference of which is shrunk a special steel rim with a wider base than normal, so that used in conjunction with tyres having a modified bead, the rim of the wheel is wider than the tread of the tyre. This results in the wall of the tyre being fully supported and not subject to side-flex, and the new wheels exert their pressure on the tread of the tyre instead of dissipating energy on the walls. This is but one of the many advantages obtained. The alloy castings are heat treated for no less than twenty hours after machining. Next, the drum is frozen and the casting re-heated, both to pre-determined temperatures, the two parts being placed on jigs under a hydraulic press, so that they are both pressed and shrunk together, at the same time, care being taken to obtain complete contact over the entire area of machined surfaces. The drum and the casting, now in one piece, are then frozen and the outer rim heated and forced over, when it locks itself solidly to the • ” spoke ” casting. The union obtained by this ” interference
fit ” is so powerful that the outer rim can be broken with a sledge hammer without causing it to part from the inner casting but, in order to give entire confidence, the whole is riveted up by the special Aerolite process.
Originally it was intended only to use these wheels for the racing single-seater Austins marketed by the Almack concern to special order, and which cost .2385.
In response to enquiries, however, it has been decided to market the wheels independently in sets of five, the cost (wheels, tyres and tubes complete) being £30.